How to save energy and reduce consumption in asphalt mixing plant from the perspective of equipment?
1. Adopt frequency conversion control system to adjust fan power
As the key equipment of asphalt mixing plant, induced draft motor has the highest energy consumption in asphalt mixing plant. Generally speaking, the power of induced draft fan will account for about 20-35% of the total power of mixing plant. If we can find ways to reduce the fan power, we can effectively reduce the energy consumption of asphalt mixing plant. General asphalt mixing plants use self-regulated induced draft motors, which use the highest power when starting up. When the mixer starts working, the fan will adjust its working efficiency from the front blade, but this adjustment is lagging and inefficient. When the mixer works at constant working power, the fan needs 30 minutes-1 hour to adjust to the best working power, This time will cause a lot of energy waste. Therefore, the management personnel of the asphalt mixing plant can consider introducing the frequency conversion control system to automatically control the fan of the asphalt mixing plant, so as to improve the working fit between the fan and the mixing plant.
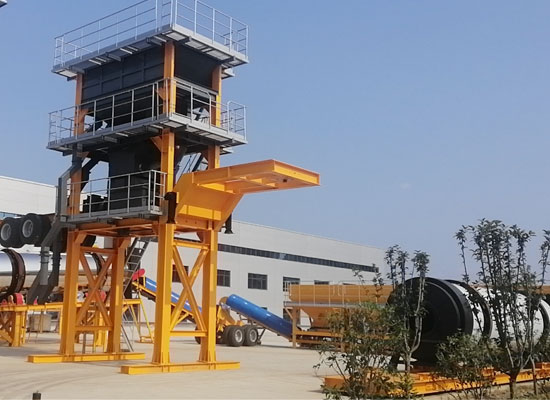
2. Maintain the pipeline system
The asphalt mixer will generate a lot of heat in the working process. At this time, it is necessary to do a good job in the thermal insulation of the mixer to prevent heat loss, which will lead to the delay of the temperature of the mixer and waste a lot of energy. Generally speaking, the mixer is equipped with a good pipeline insulation system, which can meet the needs of most mixing plants. However, if the mixer is in high-power working state for a long time and is not maintained regularly, its insulation layer will age and fall off with the increase of service life. If it is not repaired in time, it will not only cause a lot of energy consumption, Moreover, it will gradually lead to cracks in some parts of the pipeline, lead to high-temperature and high-pressure gas leakage in the pipe, greatly increase energy consumption, and even explosion accidents. Therefore, the management personnel of the asphalt mixing plant must regularly arrange the maintenance of the asphalt mixer. The specific maintenance work shall be carried out not only for the mixer itself, but also for the high-temperature pipeline, to detect whether the insulation layer on the outer wall of the pipeline is aging, whether the inner wall of the pipeline is cracked, etc.
3. Add air compressor and air storage tank
The working efficiency of asphalt mixer is directly related to the combustion efficiency of burner. There are three methods to improve the combustion efficiency of burner: adjusting the flame shape of burner, adjusting the air-oil ratio and improving the fuel atomization efficiency. The flame shape of the burner shall be ejected from the nozzle and evenly distributed around. The flame is bright without black smoke, the top of the flame does not touch the cylinder wall, and the flame does not jump or make abnormal noise. This can be achieved in most mixing plants. Air oil ratio is an important working parameter of the burner of asphalt mixer, which is generally set by the manufacturer's personnel and should not be changed easily. Therefore, in order to improve the combustion efficiency of the burner, manual atomization can be used to improve the atomization efficiency of fuel oil, so as to improve the combustion efficiency of fuel oil and reduce fuel consumption. The addition of air compressor and air storage tank can increase the pressure at the fuel injection outlet. A conventional air compressor can improve the fuel atomization efficiency by about 30%, which can effectively reduce the operating cost of asphalt mixing plant. The original oil consumption of an asphalt mixing plant is 9.42kg/t. An additional air compressor and air storage tank are invested 480000 yuan. After the transformation, the oil consumption is reduced to 7.22kg/t. After the transformation, the mixing plant can recover all the transformation costs in only two or one years, and achieve the purpose of energy conservation and emission reduction.